セレコーポレーションが手掛けるアパート「My Style」、「My Style vintage」で使われる主要な構造部材は、品質管理の行き届いた自社工場で一貫製造しています。
業界初のジルコニウム化成を採用し、環境への配慮と確かな品質、コストバランスを実現すべく、万全の検査体制のもと、自社で管理・施工していくという自社責任施工の体制を徹底しています。
今回の記事では、2019年9月に誕生したセレコーポレーションの自社工場と、ゲストの安全・オーナーの安心のために徹底されたセレのモノづくりへのこだわり、品質管理への想いをご紹介します!
まずはお気軽に
お問い合わせください。
アパート経営が初めての方もご安心ください。
お問い合わせ後は専任のコンサルタントがサポートさせていただきます。
立地――建設現場までの輸送時間短縮
セレコーポレーションは、事業エリアを“東京圏”に特化しています。
地震が多く、今後大型地震が起こりうるこの東京圏で、ゲストの安全・オーナーの安心を確保するために、さらなる新技術を開発する必要がありました。
そしてその開発した新技術を体現するために新たに建設したのが、「千葉工場」です。
東京圏の建設現場へ60分以内にアクセスできること、
またオーナー様やステークホルダーの方々にも製造工程をご覧いただき、セレの安心の技術を実際にご確認いただける距離であることを前提に工場の建設地を検討し、そんな中で出会ったのが“ちばリサーチパーク”でした。
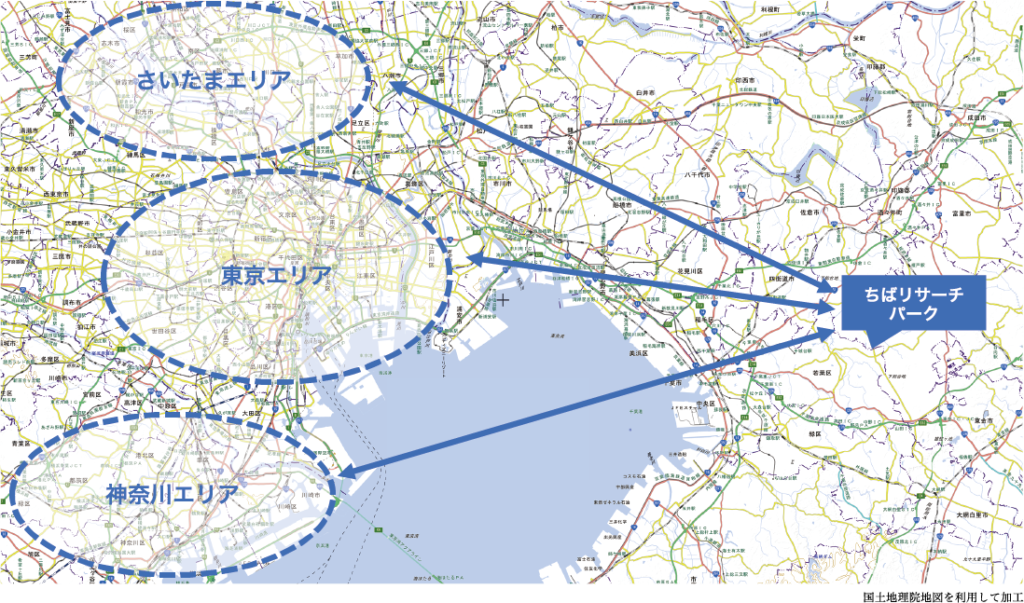
“ちばリサーチパーク”は、“研究と製造が一体となった新しいスタイルの産業用地“を目指した、三菱地所による大規模開発計画です。
都心から東関東自動車道を通って佐倉I.C.より約6km(所要時間:1時間)、自然災害のリスクを考慮した内陸部に、緑豊かで自然環境も充実しています。
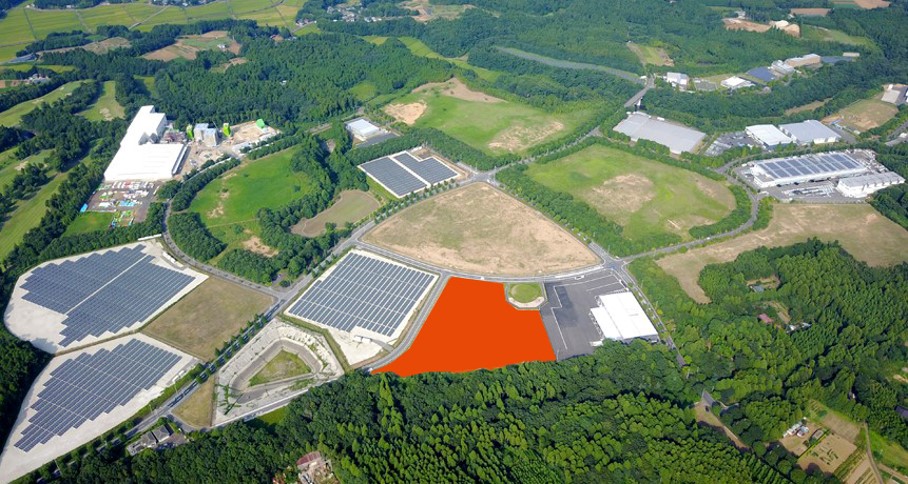
また、首都圏としては広大な約57万坪(東京ドーム42個分)もの面積を誇り、開発全体面積は1,903,518m²(麻倉ゴルフ場を含む)以上、千葉市と佐倉市にまたがってつくられています。
セレコーポレーションの千葉工場は角地の約25,000㎡(約7,500坪)で、アクセス・環境ともに理想的な製造拠点となりました。
認定・認証――厳しい審査基準をクリア
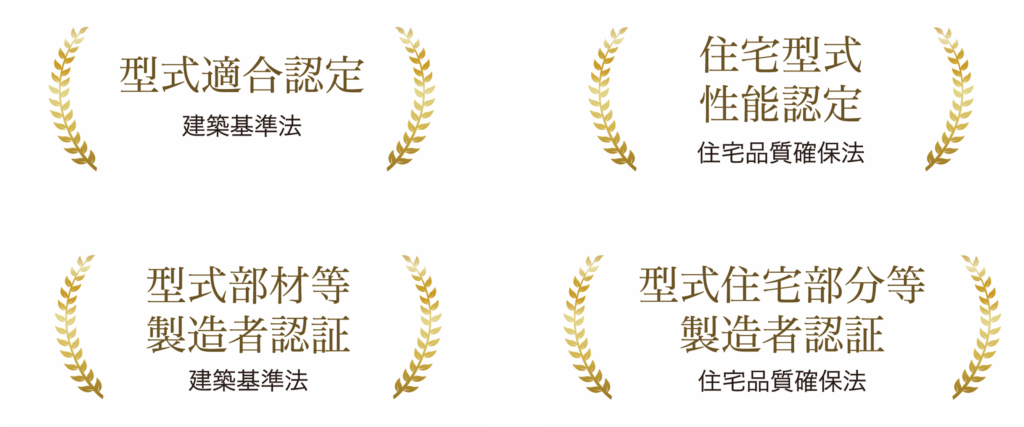
日本製鉄グループ(旧:新日鐵住金グループ)との長期にわたる共同実験や強度試験などの実験データをもとに、国土交通大臣指定の認定機関による厳しい審査をクリアし、以下の4つの認定・認証を取得しています。
・型式適合認定(建築基準法)…建物の構造、防火、設備、一般構造について予め認定を受けているもの
・住宅型式性能認定(品確法)…材料自体の耐久性、工法による劣化軽減など一定の性能を有していると認定されているもの
・型式部材等製造者認証(建築基準法)…型式適合認定を受けた建物の主要部材を製造する
・型式住宅部分等製造者認証 …住宅型式性能認定を受けた建物の主要部材を製造する
これらを全て取得している鉄骨プレハブメーカーは、セレを含めて国内8社のみです。
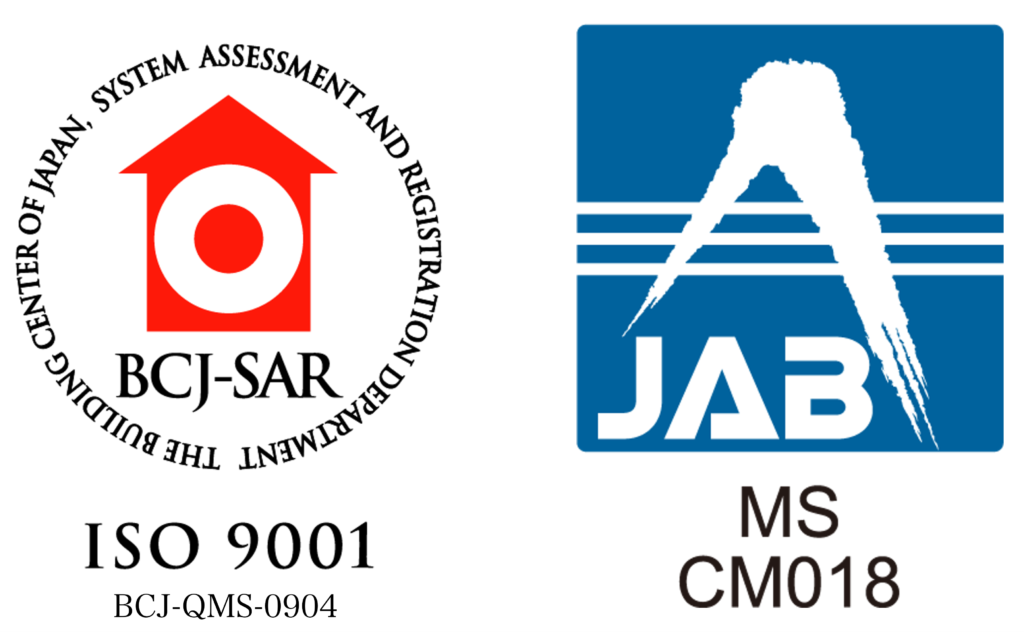
さらに、今年2022年11月1日には、千葉工場において品質マネジメントシステム(Quality Management System)の国際規格である「ISO9001」の認証を取得し、製造工程において高度で安定的な品質管理が認められました。
つまりセレが扱う建物はすべて、厳しい基準をクリアした信頼の住宅ということなのです。
製品――安心・安全のための鉄骨造
セレコーポレーションのアパートは鉄骨造に特化しています。
ゲスト(入居者)が住むアパートの耐震性を高めるために、「軽量化」そして「剛性強化」という、相矛盾する難題に取り組み、従来より約20%の軽量化、約3.6倍の剛性強化に成功しました。
構法は国土交通大臣の指定機関・財団法人日本建築センターから住宅性能表示制度の耐震最高等級である耐震等級3の認定を受けたセレオリジナルの構法「ハイテンションキューブシステム」を採用。高い安全性と優れた耐久性をハイレベルで満たしています。
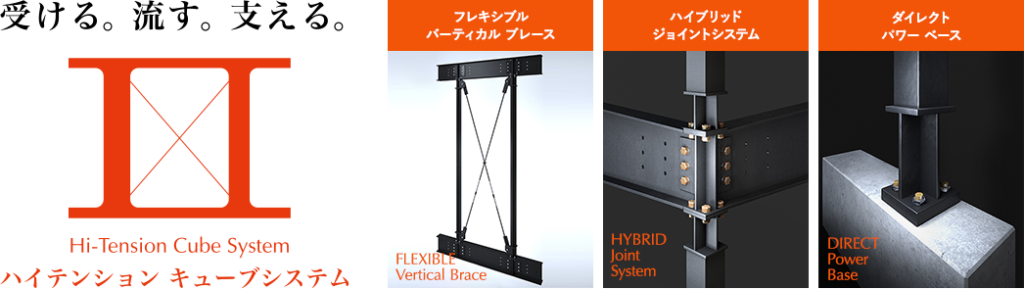
「ハイテンションキューブシステム」は、以下の3つの製品から構成されています。
●「フレキシブルバーティカルブレース(鉛直ブレース)」
フレームにブレースを直接接合させ、横から加わる“力を受け止める”
●「ハイブリット・ジョイント・システム」
梁と柱をつなぐ接続部分で、建物に加わる“力を受け流す”
●「ダイレクト・パワー・ベース」
柱を基礎のアンカーに直接接合させ、建物に加わる“力から支える”
壁、床、天井全てに独自のブレースを配置することで、あらゆる方向に応力を発揮。強力な粘りが建物の耐震性を担保します。
工場内部――建屋と設備紹介
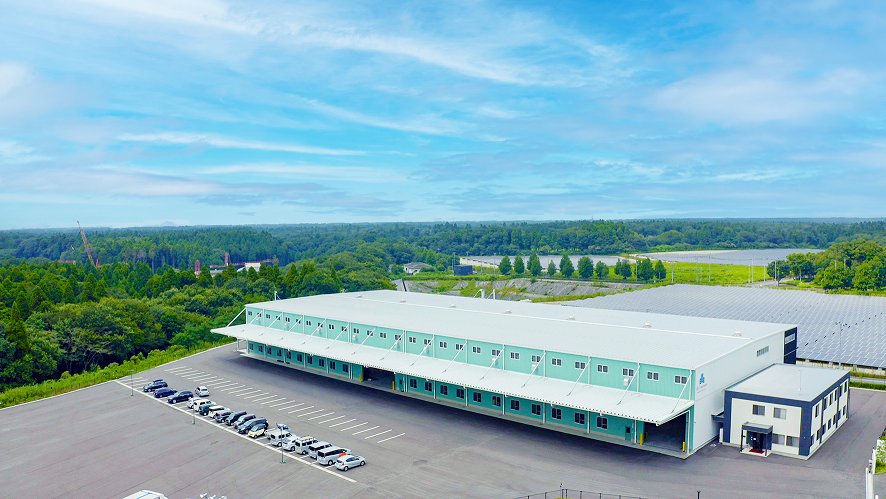
次に、工場本体建屋と設備をご紹介します。
工場建屋は約4,500㎡(奥行き約45m×幅約100m)。
出荷や受け入れが雨天時でも影響を受けにくくする、9m×100mの張り出し屋根を高度な技術で設置しています。
工場内部は、下の図のように分かれています。
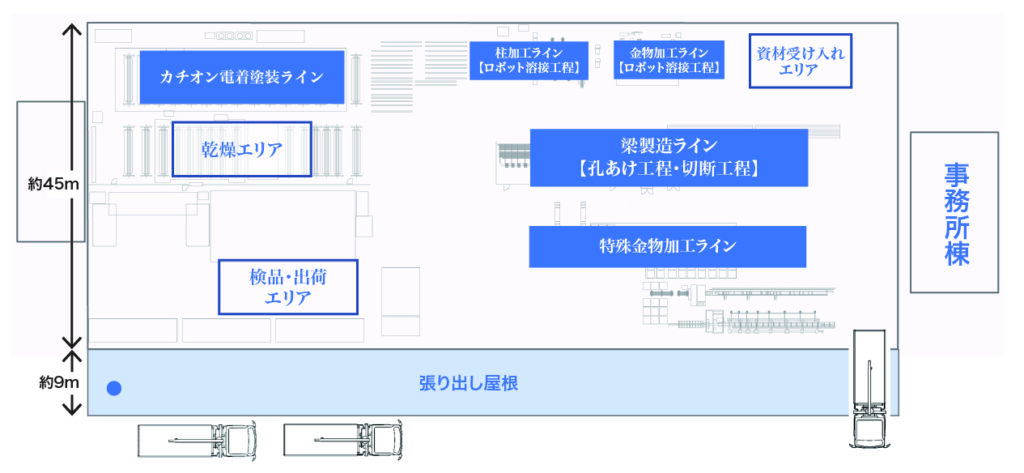
資材受け入れスペース
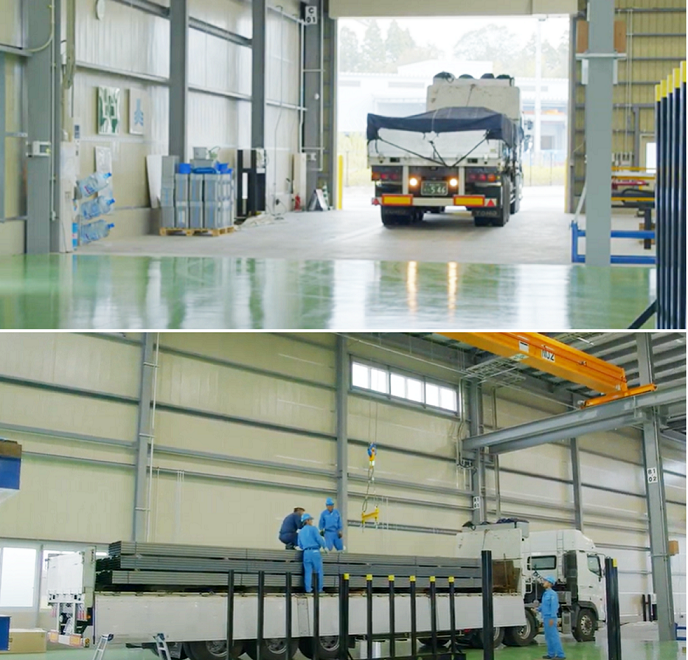
まず、資材が納入されると「資材受入スペース」へと搬入されます。
鉄骨を運ぶ20トントレーラーが直接入ってこられるほどの大きな入り口と広い車路を確保しています。
雨から守られた状態で運ばれた鉄骨は、クレーンで吊り上げられ、荷下ろしされた後に各加工ラインへと運ばれて行きます。
梁製造ライン(孔あけ工程・切断工程)
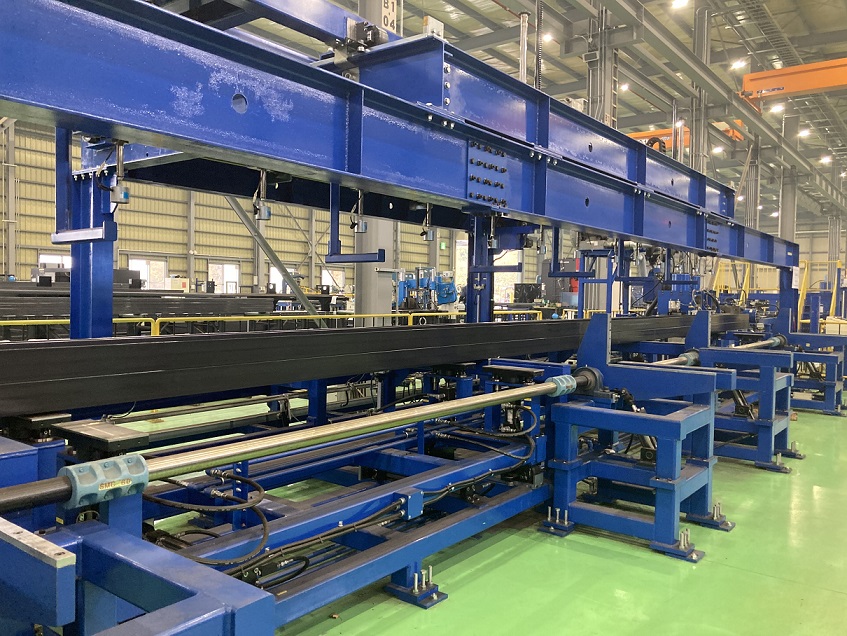
アパートの梁に孔あけや切断を行う加工ラインです。
先程の「資材受入スペース」に保管されたH鋼を、アパートごとに指定された長さに切断し、柱や金物取付用孔及びライフラインの管を通す孔あけ加工をします。
オペレーターは、一本の鋼材からアパートごとに無駄が出ないよう取り合いを検討し、プログラムし加工開始となります。
3.金物加工ライン(ロボット溶接工程)
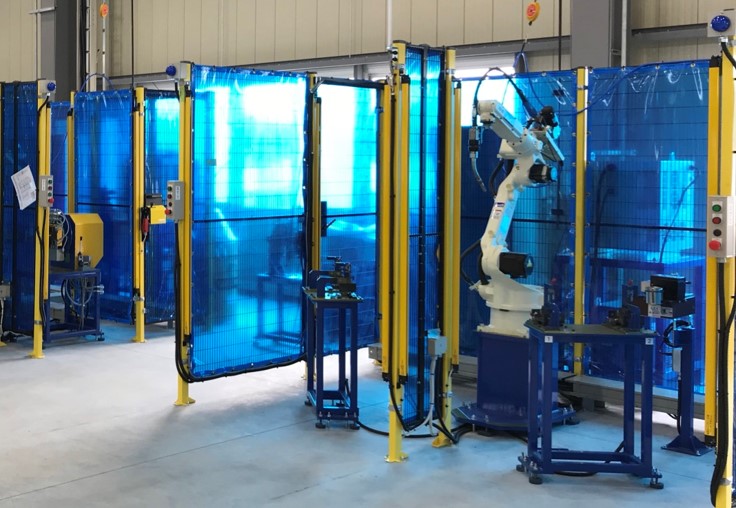
こちらは金物の溶接工程です。
プログラミングされたロボットにより、ハイテンション・キューブ・システムなどで使われる構造部材が製造されます。
4柱加工ライン(ロボット溶接工程)
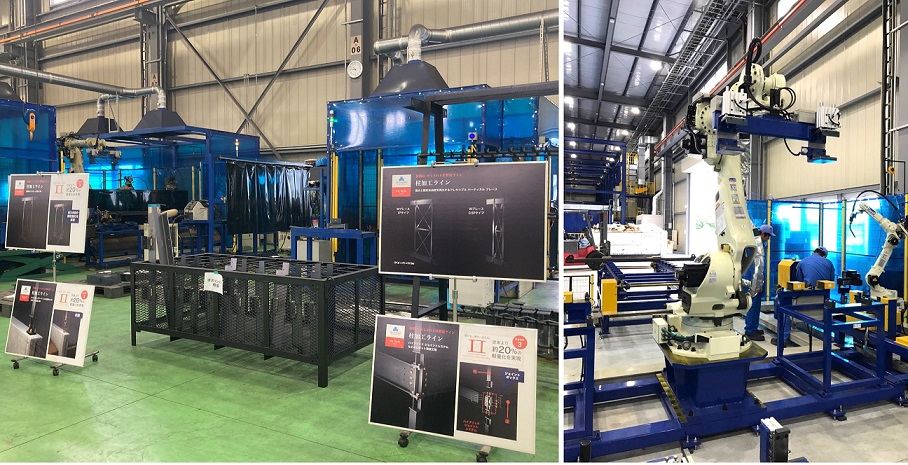
構造部材は隙間なく溶接されたあと、こちらのラインで柱に取り付けられます。
工程は完全に機械化されており、均一でむらのない品質を保ちながら一本一本作り上げていきます。
5.カチオン電着塗装ライン
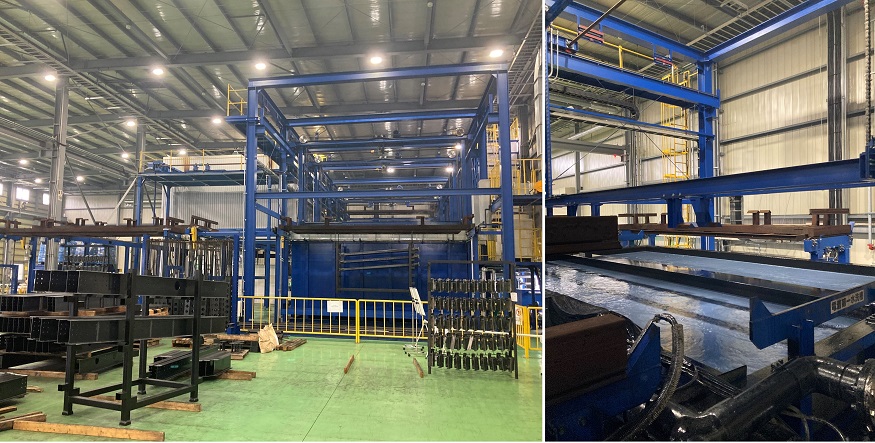
加工が終わった構造部材は、こちらの巨大な装置前に集められ、鉄の弱点である錆を防ぎ、長い年月強度を保ち続けるために塗装処理を施します。
鉄骨の住宅メーカーでは、錆を防ぐために必ず塗装処理が行われます。
刷毛で塗る、スプレーで噴射する、パウダーを吹き付けるなどその方法は様々ですが、どれも耐用年数が低く、塗装面に凹凸ができたり、厚みが不均一だったりと、セレコーポレーションが求めるクオリティには達していませんでした。
そんな中で選んだのが、“電着塗装”です。
カチオン電着塗装は、自動車のボディの塗装にも使用される薄くて頑丈な塗装です。
薄さは20ミクロン、わずかサランラップ2枚ほどでありながら、耐用年数は約75~100年といわれており、錆に強く、かつ高耐久・高耐候な部材の開発を可能にしました。
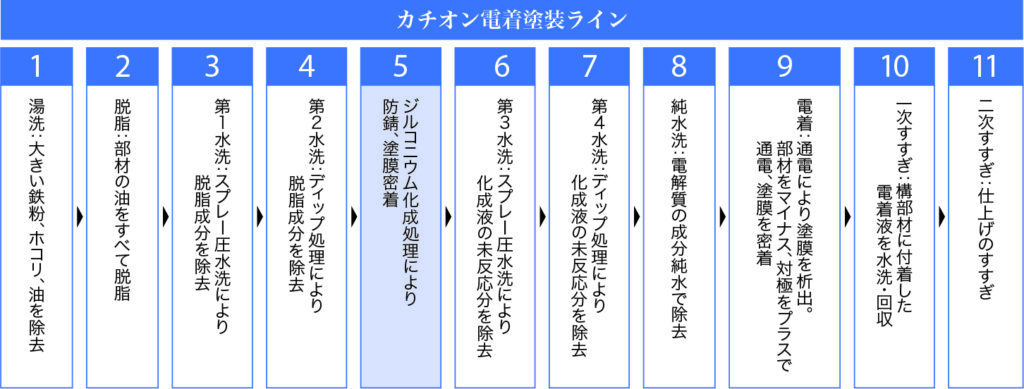
電着塗装の所要時間は約2時間半。洗浄を含む11の槽を経て、乾燥炉に入り完了します。
また、業界では初めてとなる、地球環境にやさしいジルコニウム化成を採用し、塗装との密着性を強化するとともに産業廃棄物の発生を1/10に抑えることに成功しています。
6.特殊金物加工ライン
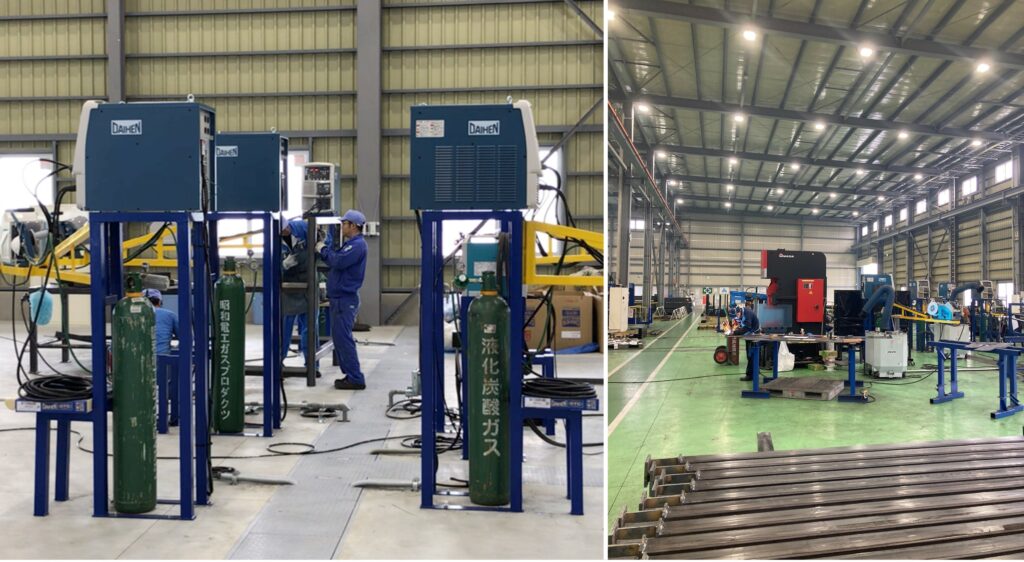
ここでは少量製造するものを手で溶接しています。
階段柱や段板、バルコニーや通路腰壁の骨組みを製造しています。
7.最終検査
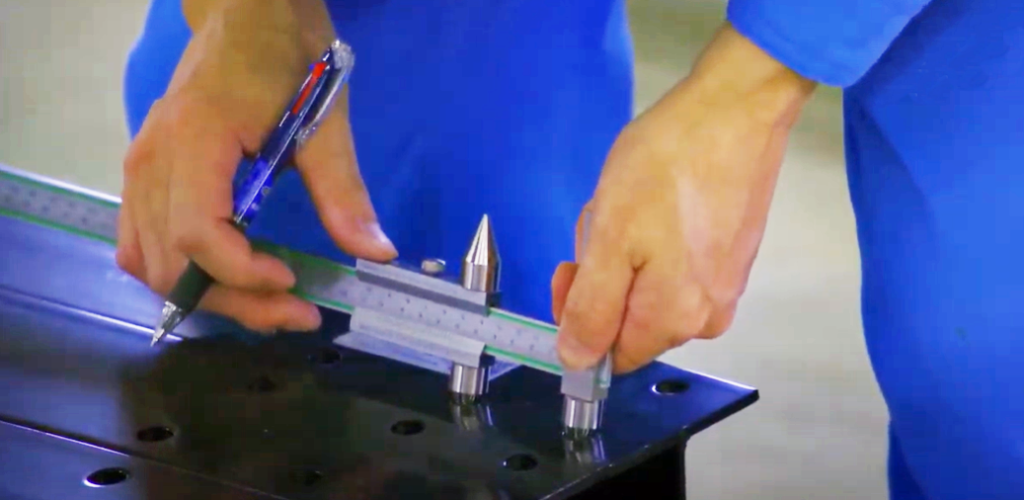
塗装を終えた構造部材は1か所に集められ、専門の係員による最終検査が行われます。
孔の大きさ、切断された長さ、塗装の厚みの均一性など、最後は人の目で細かくチェックします。
8.出荷
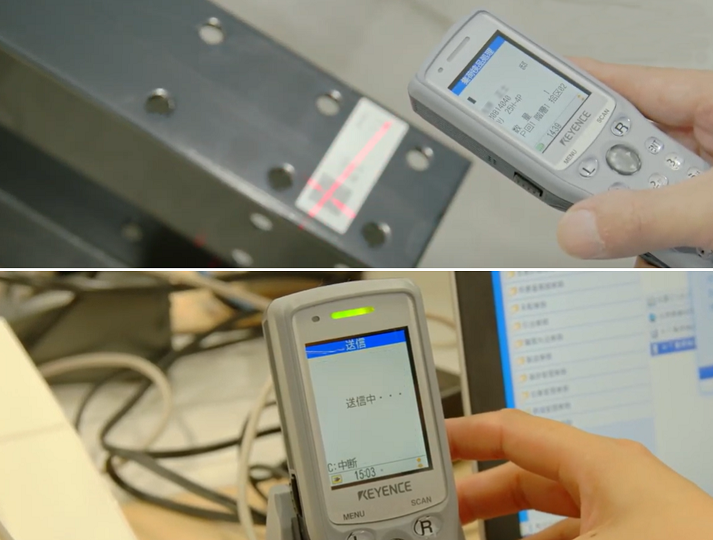
アパートごとに仕分けされたQRコードを読み取ると、事務所の端末に共有され、積み間違いや積み残しを防止防げるようになっています。
このように完全に管理された体制のもと、すべての構造部材がフォークリフトでトラックに積まれ、各アパート建築現場へと出荷されます。
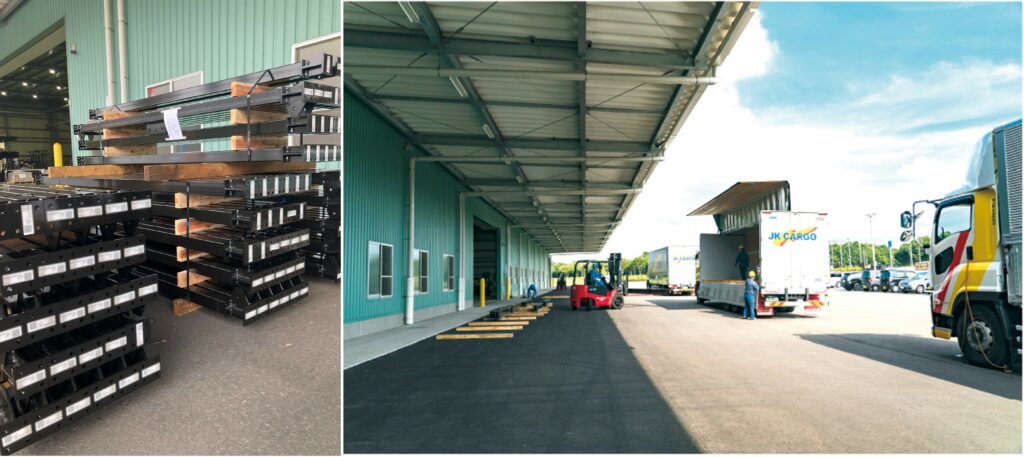
千葉工場では主要部材の製造ラインをコンピューターで制御することで、効率的な生産フローを実現しています。
高品質・高精度な構造部材の製造と、蓄積してきたノウハウから生まれたセレ独自の構法で、耐震性・耐火性・耐久性に優れたアパートを自社一貫生産しています。
自社一貫製造――ゲストの安全、オーナーの安心のために
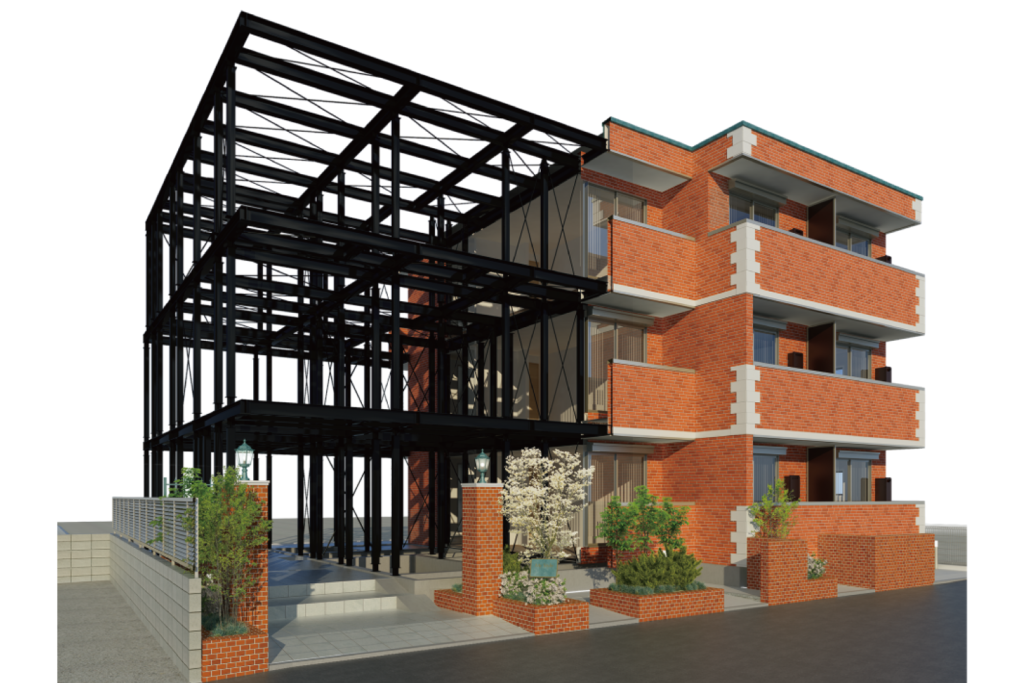
認証工場で自社一貫製造している構造部材は、長い年月をかけた様々実験を経て開発されました。
安全性・耐久性にも優れているバランスの良い構造体で「ゲストの安全」を確保し、資産価値を長期間維持することで「オーナーの安心」につながるのです。
セレコーポレーションは、人生設計の課題解決のためのコンサルティングから、自社工場での構造部材製造、自社責任施工、アフターメンテナンスまで自社一貫体制にこだわっています。
「アパート経営の専門店」として、徹底したこだわりで細部にまで責任を持ち、モノづくりに臨んでいます。
認定・認証や独自開発の建築構法、厳重な検査の実施体制などを通して、建物の安全性・信頼性を実現。ゲストの暮らしと、オーナーの長期にわたるアパート経営をハードの面からも支えていきます。
千葉工場はこちらの動画でもご紹介しています。ぜひご覧ください!
まずはお気軽に
お問い合わせください。
アパート経営が初めての方もご安心ください。
お問い合わせ後は専任のコンサルタントがサポートさせていただきます。